Der 3D-Druck als Produktionsverfahren wird auch für die Luftfahrt immer interessanter. Bauteile für die Flugzeugkabine einzelner Passagierflugzeugtypen kommen bereits aus dem 3D-Druck oder der so genannten additiven Fertigung.
Am Institut für Faserverbundleichtbau und Adaptronik des Deutschen Zentrums für Luft- und Raumfahrt (DLR) in Braunschweig untersuchen Wissenschaftler seit kurzem in einem eigens eingerichteten Labor, wie sich 3D-Druckverfahren mit bereits eingeführten Herstellungstechnologien für Verbundwerkstoffe kombinieren lassen.
Leichtbau ist gefragt
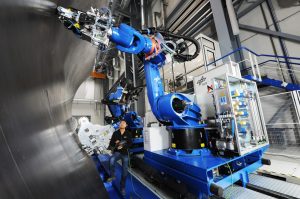
Klassische Leichtbaufertigung mit Faserablegeköpfen. So werden die im 3D-Druck produzierten Komponenten zusammengefügt. (#2)
Hintergrund ist die steigende Nachfrage nach Leichtbaustrukturen und Bauteilen aus faserverstärkten Kunststoffen in der Luft- und Raumfahrt, aber auch in anderen Branchen wie dem Automobilbau oder der Produktion von Windkraftanlagen. Das Institut erforscht nun, wie sich diese so genannten ‚Additive Composite Structures‘ (AddComS) effizient herstellen lassen. Das sind Strukturen, die aus einem Materialverbund bestehen. Ein Teil der Schicht kommt aus dem 3D-Druck, eine weitere Komponente ist ein konventionell hergestelltes Faserverbund-Bauteil.
„Welches 3D-Druck-Verfahren sich für welchen Anwendungsfall am besten eignet, wollen wir nun genauer untersuchen“, erklärt Prof. Hans Peter Monner vom DLR-Institut für Faserverbundleichtbau und Adaptronik in Braunschweig. „Mit einem neuen 3D-Druck-Labor haben wir uns nun die notwendige Basis geschaffen, um unser Forschungsfeld AddComS TM voranzutreiben.“ Die Forscher haben bereits erste Bauteile im Labor produziert.
Darunter sind extrem leichte Flügelrippen für ein solarelektrisch betriebenes Höhenflugzeug, das als fliegende Relaisplattform für Kommunikationsverbindungen oder zur Erdbeobachtung dienen kann. Die Flügelrippen entstehen, indem ein thermoplastischer, also hitzeverformbarer Kunststoff auf Carbonendlosfasern gedruckt wird. Dieses neue Verfahren hat klare Vorteile: „Nach konventioneller Bauart werden die Rippen ausgefräst. Der 3D-Druck ermöglicht uns dagegen eine kraftflussgerechte Verwendung der Fasern, wodurch weniger Fasern und Kunststoff verbaut werden müssen“, erklärt Prof. Monner. „Das macht das Bauteil noch leichter.“
Was der 3D-Druck für die Luftfahrt leisten kann
Durch den 3D-Druck können die tragenden Fasern so angeordnet werden, dass sie den Wegen folgen, die die mechanische oder kinetische Energie durch ein Bauteil nimmt. Das ist mit herkömmlichen Verfahren wie Fräsen, Bohren oder Gießen nicht möglich. Auf diese Weise lässt sich das Material einsparen, durch das keine Kräfte fliessen.
Auch formveränderliche Strukturen lassen sich so herstellen. Wenn man feste und flexible Materialien kombiniert, können beispielsweise formvariable Flügelkanten hergestellt werden. Diese Kanten enthalten elastische, über Luftdruckveränderungen gesteuerte Zellen, deren Schrumpfen oder Wachsen die Form der Flügelkante verändert. So ließen sich herkömmliche Klappensysteme ersetzen, mit denen beispielsweise bei der Landung gebremst oder das Flugzeug gesteuert wird. Bisher erfordern diese Klappensysteme eine aufwendige mechanische Struktur mit Stellmotoren, Steuerleitungen, hydraulischen oder pneumatischen Systemen und konstruktiven Vorrichtungen im Flügel. Formvariable Bauteile könnten hier wiederum Material und damit Gewicht einsparen helfen.
Am DLR-Institut werden die 3D-Drucktechnologien „Fused Deposition Modeling“ (FDM) und „Multi Jet Modeling“ (MJM) angewendet.
Fused Deposition Modeling
„Fused Deposition Modeling“ wird im Deutschen als Schmelzschichtung bezeichnet. Dabei wird das Werkstück schichtweise aus einem schmelzfähigen Kunststoff aufgebaut.
Bei diesem Verfahren wird zunächst ein Raster aus extrem kleinen Punkten aufgetragen. Darauf setzt der Drucker dann weitere Schichten, um den Körper aufzubauen. Der 3D-Drucker fährt Zeile für Zeile eine Druckebene ab und wiederholt diesen Vorgang dann auf der nächsthöheren Ebene. So entstehen viele, je nach Anwendung zwischen 0,025 mm und 1, 25 mm dicke Schichten.
Entwickelt hat dieses Verfahren S. Scott Crump in den 1980er Jahren; kommerziell verwertet wird es seit den 1990er Jahren.
Multi-Jet Modeling
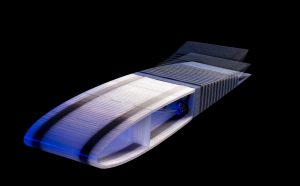
Die gedruckte und formveränderliche Flügelhinterkante kommt ohne herkömmliche Klappensysteme aus. (#4)
„Multi-Jet Modeling“ baut ein Werkstück ebenfalls schichtweise auf. Hierbei besteht der Druckkopf wie der eines Tintenstrahldruckers aus mehreren linear angeordneten Düsen. Dieses Verfahren ermöglicht extrem feine Tröpfchen, sodass auch extrem feine Details hergestellt werden können.
Bildnachweis: © alle DLR